Evaluating the Impact of Lean Management on Material Resource Efficiency
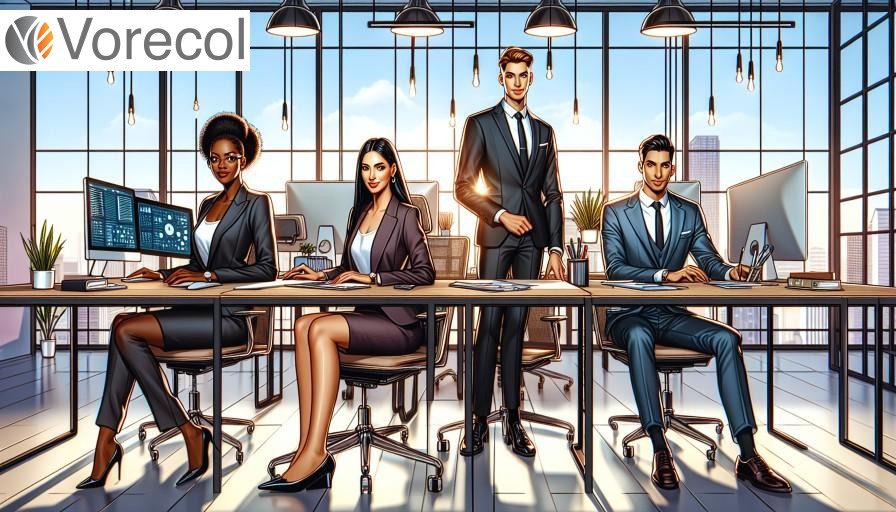
- 1. Introduction to Lean Management Principles
- 2. Understanding Material Resource Efficiency
- 3. Key Metrics for Evaluating Efficiency in Lean Practices
- 4. Case Studies: Successful Lean Implementations
- 5. Challenges in Measuring Material Resource Efficiency
- 6. Strategies for Enhancing Resource Efficiency through Lean Techniques
- 7. Future Trends in Lean Management and Resource Optimization
- Final Conclusions
1. Introduction to Lean Management Principles
In the bustling world of manufacturing, the principles of Lean Management have emerged as a transformative force, revolutionizing the way companies operate. Originating from the Toyota Production System in the mid-20th century, Lean Management focuses on maximizing value by eliminating waste, enhancing efficiency, and fostering a culture of continuous improvement. According to a study by the Lean Enterprise Institute, organizations that adopt Lean practices see an average reduction in waste by 30%, significantly improving their bottom line. Companies like Boeing have reported an impressive 20% increase in productivity after implementing Lean principles, showcasing the profound impact that such methodologies can have on operational excellence.
Imagine a factory floor bustling with activity, yet every worker knows their role in reducing inefficiencies and improving processes. This is the reality for many organizations that have adopted Lean Management. A survey by the manufacturing consultancy firm LNS Research indicates that 63% of companies practicing Lean have experienced enhanced customer satisfaction, a testament to the methodology's focus on delivering value. Moreover, a staggering 51% of firms have noted quicker product development cycles as a direct benefit of Lean practices, allowing them to respond to market demands with agility. As we delve deeper into the foundational principles of Lean Management, it becomes clear that these strategies not only streamline operations but also create an engaged workforce, poised for success in a competitive landscape.
2. Understanding Material Resource Efficiency
In a world where resource scarcity is becoming increasingly apparent, understanding material resource efficiency has taken the center stage in corporate sustainability efforts. Picture a thriving manufacturing company that decides to audit its material usage. Through this deep dive, they discover that 30% of the raw materials they purchase end up as waste. This shocking revelation leads them to adopt a more circular approach, realizing that improving efficiency not only minimizes waste but also enhances profitability. According to a 2022 report by the Global Reporting Initiative, companies that prioritize resource efficiency experience an average cost savings of 15% over five years, a compelling incentive for industries aiming to shrink their environmental footprint while bolstering their bottom line.
Imagine another scenario with a tech startup that committed to sustainable practices from its inception. By investing in material resource efficiency strategies, such as reusing components in their production process, they increased their productivity by 20% while simultaneously reducing their material costs by 25%. Research from the World Economic Forum highlights that enhancing material efficiency across industries could potentially yield economic benefits exceeding $3 trillion globally by 2030. This narrative serves to illustrate not just the necessity, but also the viability of adopting innovative resource efficiency practices that promote environmental stewardship while fueling economic growth.
3. Key Metrics for Evaluating Efficiency in Lean Practices
In the quest for operational excellence, organizations employing lean practices have identified several key metrics that act as guiding stars in their efficiency journeys. One such metric is Overall Equipment Effectiveness (OEE), which has gained traction across manufacturing sectors. A recent study by the Lean Enterprise Institute reported that companies with strong OEE performance save up to 20% on production costs. This metric helps businesses understand the availability, performance, and quality of their equipment—crucial factors in revealing bottlenecks that hinder productivity. Imagine a company that managed to elevate its OEE from 65% to an impressive 85%, translating this 20% improvement into an annual savings of over $1 million!
Additionally, First Pass Yield (FPY) stands out as another vital metric, representing the percentage of products manufactured correctly without rework or defects. According to the American Society for Quality, organizations with a high FPY often achieve up to 30% higher customer satisfaction rates due to fewer errors and faster delivery times. For instance, consider a tech startup that, after implementing lean methodologies, increased its FPY from 75% to 95%. This leap not only enhanced customer satisfaction but also propelled the company's market share by 15% in just one fiscal year. These metrics underscore how leveraging lean practices can dramatically improve efficiency and drive organizational success, revealing a narrative of transformation and growth that resonates across industries.
4. Case Studies: Successful Lean Implementations
In the bustling world of manufacturing, one company stands out for its remarkable transformation through lean implementation: Toyota. In the early 2000s, the company focused on eliminating waste and improving efficiency by adopting the Lean methodology, which resulted in a staggering 50% reduction in production time. A study by the Lean Enterprise Institute revealed that companies that followed lean practices reported a 30% increase in productivity, demonstrating that Toyota's commitment to these principles not only enhanced their operational efficiency but also set a benchmark for competitors. As a result, Toyota's market share surged, ultimately leading to its position as the world's largest automaker, a testament to the power of lean principles in driving success.
Another captivating example can be found in the healthcare sector, where Virginia Mason Medical Center in Seattle adopted lean practices to enhance patient care. By introducing the Toyota Production System into their operations, they were able to reduce patient wait times by 40%, significantly improving patient satisfaction scores. A 2015 study published in the Journal of Healthcare Management noted that organizations implementing lean initiatives encountered a 39% decrease in patient flow variability. These statistics demonstrate how the integration of lean practices not only streamlines processes but also creates a culture of continuous improvement, ultimately leading to better outcomes for both patients and providers. The journey of Virginia Mason illustrates that lean isn't just a technique for manufacturing; it’s a transformative philosophy that can lead to groundbreaking results across various industries.
5. Challenges in Measuring Material Resource Efficiency
Measuring material resource efficiency presents a formidable challenge for businesses striving to balance economic growth with environmental sustainability. According to a 2022 report by the World Economic Forum, approximately 60% of the world’s natural ecosystems are being degraded due to industrial activities. In this context, companies face the daunting task of quantifying their resource consumption and understanding the real impact of their operations. A study published in the Journal of Industrial Ecology highlighted that less than 30% of organizations effectively track their material usage, resulting in significant tidbits of waste going unnoticed. This lack of visibility not only hinders their ability to make informed decisions but also opens the door for potential liabilities and reputational risks as consumers increasingly demand sustainable practices.
Moreover, the complexity of supply chains adds another layer of difficulty in measuring resource efficiency. A report by McKinsey revealed that supply chain emissions account for more than 80% of a company's greenhouse gas emissions, yet only 10% of firms are equipped to measure them accurately. The 2023 Corporate Sustainability Reporting Directive underlines this issue by imposing stricter regulations on companies regarding their resource usage and sustainability metrics. As businesses grapple with fragmented data across multiple regions and suppliers, many find themselves lost in a sea of numbers, unable to derive actionable insights. Consequently, firms that prioritize resource efficiency are not just improving their bottom line but are also positioning themselves as leaders in an ever-evolving market focused on environmental stewardship.
6. Strategies for Enhancing Resource Efficiency through Lean Techniques
In the bustling halls of an automotive manufacturing plant, a manager named Sarah faced the daunting challenge of reducing waste while boosting production efficiency. By implementing lean techniques, her team was able to eliminate 30% of non-value-adding activities within just six months. Studies indicate that companies adopting lean strategies can increase operational efficiency by approximately 25%. For instance, a report from the Lean Enterprise Institute revealed that organizations implementing these methods experienced up to a 50% reduction in lead times and a nearly 80% increase in customer satisfaction. By utilizing tools such as value stream mapping and the 5S methodology, Sarah's team not only streamlined their processes but also fostered a culture of continuous improvement.
As Sarah witnessed the transformation within her plant, she shared her story with her industry peers, highlighting the profound impact of fostering employee engagement on resource efficiency. Research shows that companies with highly engaged teams reduce their resource consumption by an average of 34%. For instance, Toyota has demonstrated that empowering frontline workers to identify inefficiencies led to a staggering 60% reduction in defects and an impressive 35% increase in productivity. By embracing lean principles alongside a focus on workforce engagement, organizations can uncover hidden efficiencies that yield substantial savings. In a world where every drop of wasted resource counts, the ripple effect of lean techniques can propel a company toward sustainable success.
7. Future Trends in Lean Management and Resource Optimization
In a world where efficiency is paramount, lean management and resource optimization are set to undergo transformative changes. A study by McKinsey found that 80% of organizations believe that improving efficiency will be vital for their future success. Enter the age of smart technologies; companies like Toyota and GE are integrating AI and IoT into their processes, reducing waste by up to 30% while enhancing productivity. For instance, a recent report showed that GE's adoption of digital twin technology resulted in a 10% increase in operational efficiency. As these trends continue to unfold, organizations that fail to adapt risk falling behind in an increasingly competitive market.
The shift towards sustainability is another driving force behind future trends in lean management. According to a survey by Deloitte, 70% of executives acknowledge that sustainable practices are critical for long-term success. Companies such as Unilever have tapped into this trend, committing to a 100% sustainable sourcing model, which not only boosts their brand image but also increases annual sales by 20%. Moreover, research from the International Journal of Production Research indicates that implementing lean principles alongside sustainability initiatives can lead to an impressive 50% reduction in material costs. As businesses navigate these evolving landscapes, the integration of lean practices and a commitment to sustainability will redefine industry standards and operational excellence.
Final Conclusions
In conclusion, the evaluation of Lean Management's impact on material resource efficiency reveals significant benefits that extend across various industries. By prioritizing waste reduction and streamlining processes, Lean methodologies not only enhance operational performance but also promote sustainable resource use. Companies that adopt Lean practices report improved inventory turnover, reduced material costs, and minimized environmental footprints. These advantages showcase how Lean principles can lead to more efficient resource management, all while maintaining quality and customer satisfaction.
Moreover, the successful implementation of Lean Management requires a cultural shift within organizations, emphasizing continuous improvement and employee engagement. As companies increasingly face pressures to operate sustainably, integrating Lean strategies becomes not just beneficial, but essential. This alignment not only enables businesses to thrive in competitive markets but also contributes to broader environmental goals. Ultimately, the intersection of Lean Management and material resource efficiency presents a compelling case for organizations seeking to innovate while being responsible stewards of the planet's resources.
Publication Date: August 28, 2024
Author: Gestiso Editorial Team.
Note: This article was generated with the assistance of artificial intelligence, under the supervision and editing of our editorial team.
💡 Would you like to implement this in your company?
With our system you can apply these best practices automatically and professionally.
PsicoSmart - Psychometric Assessments
- ✓ 31 AI-powered psychometric tests
- ✓ Assess 285 competencies + 2500 technical exams
✓ No credit card ✓ 5-minute setup ✓ Support in English
💬 Leave your comment
Your opinion is important to us