What are the best measurement tools for assessing the utilization of material resources in manufacturing industries?
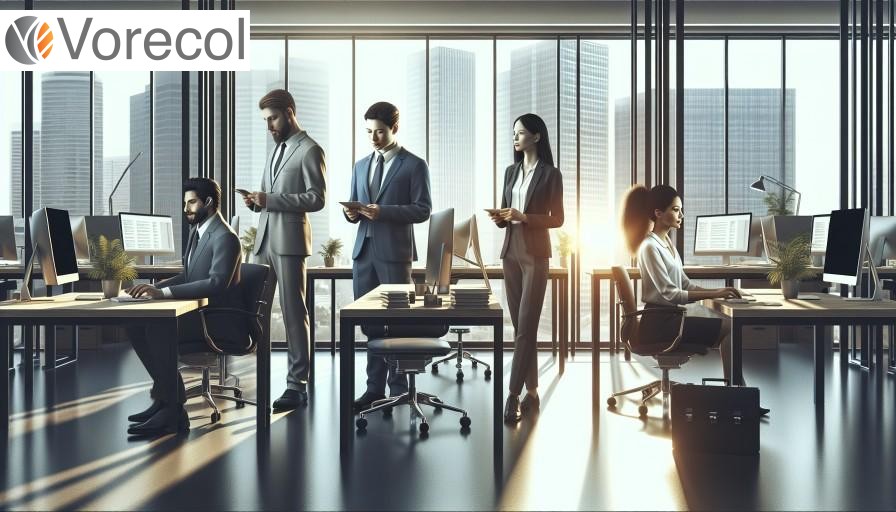
- 1. "Exploring the Top Measurement Tools for Evaluating Material Resource Management in Manufacturing"
- 2. "Efficient Methods for Assessing Material Resource Utilization in Manufacturing Industries"
- 3. "Comparing the Most Effective Measurement Tools for Optimizing Material Usage in Manufacturing"
- 4. "Measuring the Impact: Tools to Evaluate Material Resource Efficiency in Manufacturing"
- 5. "Enhancing Sustainability: Key Tools for Assessing Material Resource Utilization in Manufacturing"
- 6. "Improving Resource Management: Essential Measurement Tools for Manufacturing Industries"
- 7. "Analyzing Material Resource Utilization: A Guide to the Best Measurement Tools for Manufacturers"
- Final Conclusions
1. "Exploring the Top Measurement Tools for Evaluating Material Resource Management in Manufacturing"
In the realm of manufacturing, the evaluation of material resource management plays a pivotal role in overall operational efficiency and sustainability. One notable case is that of Toyota Motor Corporation, a pioneer in lean manufacturing principles. Toyota's approach to material resource management emphasizes just-in-time inventory systems and continuous improvement through tools like the Kanban system. This has enabled them to minimize waste, optimize production processes, and maintain high product quality. As a result, Toyota has solidified its position as one of the top automobile manufacturers globally, setting a benchmark for efficient material resource management in the industry.
Another compelling example comes from IKEA, the Swedish furniture giant renowned for its innovative approach to supply chain management. IKEA leverages advanced technology and data analytics to track and evaluate material resources throughout its expansive global operations. By implementing sophisticated tools such as RFID technology and inventory management software, IKEA has successfully optimized material usage, reduced costs, and enhanced sustainability practices. This strategic focus on measuring and analyzing material resource management has not only contributed to IKEA's financial success but also bolstered its reputation as a leader in sustainable business practices.
For readers facing similar challenges in evaluating material resource management in manufacturing, it is essential to prioritize the adoption of advanced measurement tools and technologies. Utilizing software systems like Enterprise Resource Planning (ERP) platforms, Material Requirements Planning (MRP) systems, and data analytics software can provide valuable insights into material utilization, inventory levels, and supply chain efficiency. Regular monitoring and analysis of key performance indicators related to material resource management are crucial for identifying opportunities for improvement and driving operational excellence. Additionally, fostering a culture of continuous improvement and employee engagement in material resource management processes can lead to sustainable long-term success in manufacturing operations.
2. "Efficient Methods for Assessing Material Resource Utilization in Manufacturing Industries"
Assessing material resource utilization in manufacturing industries is a critical aspect in driving operational efficiency and sustainability. One prime example comes from General Motors (GM), which implemented a sophisticated data analytics system to monitor and analyze the flow and utilization of materials throughout their production processes. By tracking key metrics such as raw material consumption, waste generation, and production yields in real-time, GM was able to identify inefficiencies and implement targeted measures to optimize resource usage. This approach not only improved their environmental performance but also led to significant cost savings.
Another noteworthy case is that of Tesla, a pioneer in the electric vehicle industry. Tesla has revolutionized the manufacturing process by implementing advanced technologies such as automated robots and AI-driven systems to streamline material resource utilization. Through careful planning and utilization of sustainable materials, Tesla has been able to achieve groundbreaking levels of efficiency in their production lines while reducing waste and environmental impact. By continuously monitoring and evaluating their material usage, Tesla has set a benchmark for other manufacturers to adopt sustainable practices in their operations. For readers facing similar challenges in assessing material resource utilization, it is crucial to invest in data-driven tools and technologies that provide real-time insights into resource flows. Conducting regular audits and implementing key performance indicators specific to material usage can help identify areas for improvement and drive efficient resource utilization. Additionally, fostering a culture of sustainability within the organization and promoting collaboration between departments can further enhance decision-making processes related to material resource management. Ultimately, by adopting a proactive and data-driven approach, businesses can achieve greater efficiency and sustainability in their manufacturing practices.
3. "Comparing the Most Effective Measurement Tools for Optimizing Material Usage in Manufacturing"
In today's competitive manufacturing landscape, optimizing material usage is crucial for reducing costs and improving efficiency. One company that has excelled in this area is BMW. By implementing advanced measurement tools such as Radio-Frequency Identification (RFID) technology and automated inventory tracking systems, BMW has been able to precisely monitor and control the flow of materials throughout their production process. This has not only led to significant cost savings but has also resulted in a more sustainable approach to manufacturing.
Another organization that has successfully utilized effective measurement tools for material optimization is Tesla. The electric vehicle giant has integrated sophisticated data analytics and machine learning algorithms into their production processes to accurately forecast material requirements and identify areas for improvement. By continuously analyzing data and adjusting their strategies, Tesla has been able to streamline their material usage, minimize waste, and enhance overall operational efficiency. For readers facing similar challenges in their manufacturing operations, it is recommended to invest in advanced measurement technologies such as IoT sensors, data analytics software, and real-time monitoring systems. By leveraging these tools, companies can gain valuable insights into their material usage patterns, identify bottlenecks, and make informed decisions to optimize their manufacturing processes effectively.
4. "Measuring the Impact: Tools to Evaluate Material Resource Efficiency in Manufacturing"
Every company striving for sustainable production practices recognizes the importance of measuring the impact of material resource efficiency in manufacturing. One notable case is that of Tesla Inc., a pioneering electric vehicle manufacturer. Tesla has implemented advanced tools and technologies to analyze and optimize their material resource efficiency throughout the manufacturing process. By incorporating cutting-edge software and data tracking systems, Tesla can accurately evaluate the environmental footprint of their production operations and identify areas for improvement. This commitment to measuring impact has not only enhanced Tesla's sustainability performance but has also boosted their reputation as an industry leader in eco-conscious manufacturing.
Another compelling example is the clothing brand Patagonia, which has set a high standard for material resource efficiency in the apparel industry. Patagonia utilizes a comprehensive set of tools, including lifecycle assessment software and waste tracking mechanisms, to evaluate the environmental impact of their manufacturing practices. By measuring factors such as water usage, energy consumption, and waste generation, Patagonia can pinpoint opportunities to enhance efficiency and reduce their ecological footprint. This strategic approach has positioned Patagonia as a frontrunner in sustainable fashion and has resonated with environmentally conscious consumers worldwide.
For readers navigating similar challenges in measuring material resource efficiency in manufacturing, it is essential to leverage available tools and technologies to track and evaluate key performance indicators. Implementing lifecycle assessment software, waste tracking systems, and energy monitoring tools can provide valuable insights into the environmental impact of production processes. It is also crucial to set clear sustainability goals, regularly monitor progress, and continuously seek opportunities for improvement. By adopting a data-driven approach and prioritizing material resource efficiency, companies can not only reduce their environmental footprint but also drive operational efficiency and enhance their competitive advantage in an increasingly eco-conscious market.
5. "Enhancing Sustainability: Key Tools for Assessing Material Resource Utilization in Manufacturing"
Sustainability in manufacturing has become a top priority for businesses looking to reduce their environmental footprint and boost efficiency. One key tool for assessing material resource utilization in manufacturing is the Material Flow Cost Accounting (MFCA) method. This method involves tracking the flow of materials within a manufacturing process to identify inefficiencies and pinpoint areas where waste can be minimized. A real-life example of a company that has successfully implemented this approach is Toyota. By using MFCA, Toyota was able to reduce waste and streamline their manufacturing processes, leading to significant cost savings and environmental benefits.
Another valuable tool for enhancing sustainability in manufacturing is Life Cycle Assessment (LCA). LCA involves analyzing the environmental impact of a product or process throughout its entire lifecycle, from raw material extraction to end-of-life disposal. Patagonia, a renowned outdoor clothing company, is a great example of a company that has leveraged LCA to improve sustainability. By conducting LCAs on their products, Patagonia has been able to identify areas for improvement in material sourcing, production processes, and end-of-life options, allowing them to create more eco-friendly products. For readers looking to enhance sustainability in their manufacturing processes, it is recommended to start by conducting a thorough assessment of material resource utilization using tools like MFCA and LCA. By understanding the flow of materials and the environmental impact of their processes, businesses can make informed decisions to optimize resource utilization and reduce waste, ultimately leading to a more sustainable and profitable operation.
6. "Improving Resource Management: Essential Measurement Tools for Manufacturing Industries"
Improving resource management is a crucial aspect for manufacturing industries to enhance efficiency and productivity. One real case that exemplifies the importance of measurement tools in this area is the success story of Siemens AG. The multinational conglomerate implemented advanced data analytics and real-time monitoring systems to optimize their resource allocation, leading to a significant reduction in waste and production costs. This strategic approach not only improved their bottom line but also positioned Siemens as a leader in sustainable manufacturing practices.
Another compelling example is the experience of Toyota Motor Corporation. Through the implementation of the Just-In-Time inventory system and Total Quality Management principles, Toyota revolutionized resource management in the automotive industry. By closely monitoring production processes and fine-tuning resource utilization, Toyota achieved remarkable efficiency gains and established a reputation for lean manufacturing practices. These real-world cases highlight the transformative impact that effective measurement tools can have on resource management in manufacturing industries.
For readers facing similar challenges in resource management, it is essential to leverage technology and data analytics to identify inefficiencies and streamline operations. Adopting a continuous improvement mindset, like Siemens and Toyota, can drive ongoing enhancements in resource utilization. Additionally, investing in employee training and fostering a culture of innovation and collaboration can further optimize resource management practices. By integrating measurement tools with strategic planning and organizational development, manufacturing industries can unlock new levels of efficiency and competitiveness in today's dynamic market environment.
7. "Analyzing Material Resource Utilization: A Guide to the Best Measurement Tools for Manufacturers"
Material resource utilization is a crucial aspect of manufacturing operations, with the efficiency of resource management directly impacting a company's bottom line. Various tools and techniques are available to help manufacturers analyze and optimize their material resource utilization. One notable example is the case of Boeing, a leading aerospace company that implemented a sophisticated material resource planning system to streamline their production process. By accurately tracking material usage and inventory levels in real-time, Boeing was able to minimize waste, reduce costs, and improve overall operational efficiency. This successful implementation serves as a testament to the importance of utilizing advanced measurement tools in the manufacturing industry.
Another compelling example comes from Toyota, a renowned automotive manufacturer known for its lean production principles. Toyota has embraced tools such as Value Stream Mapping and Just-in-Time inventory management to carefully monitor and optimize material resource utilization across its operations. By continuously analyzing production processes and identifying areas for improvement, Toyota has been able to enhance productivity, reduce lead times, and enhance sustainability efforts. Manufacturers looking to emulate Toyota's success should consider adopting similar measurement tools and continuously seek ways to drive efficiencies in their material resource utilization practices. Developing a culture of continuous improvement and data-driven decision-making is essential for achieving long-term success in maximizing resource utilization in manufacturing processes.
Final Conclusions
In conclusion, when it comes to measuring the utilization of material resources in manufacturing industries, it is clear that there is no one-size-fits-all solution. Different tools and techniques have their own strengths and limitations, and it is important for companies to carefully evaluate their specific needs and goals when choosing the right measurement tool. From traditional methods such as material balance analysis to more advanced technologies like Internet of Things (IoT) sensors and data analytics, there is a wide range of options available for assessing material resource utilization.
Furthermore, it is evident that the best approach for measuring material resource utilization in manufacturing industries is a combination of both quantitative and qualitative methods. By considering multiple factors such as waste generation, energy consumption, and production efficiency, companies can gain a comprehensive understanding of their resource utilization patterns and identify areas for improvement. Ultimately, the key to effective resource management lies in implementing a holistic measurement strategy that not only tracks material usage but also drives continuous improvement and sustainability in manufacturing operations.
Publication Date: August 28, 2024
Author: Gestiso Editorial Team.
Note: This article was generated with the assistance of artificial intelligence, under the supervision and editing of our editorial team.
💡 Would you like to implement this in your company?
With our system you can apply these best practices automatically and professionally.
PsicoSmart - Psychometric Assessments
- ✓ 31 AI-powered psychometric tests
- ✓ Assess 285 competencies + 2500 technical exams
✓ No credit card ✓ 5-minute setup ✓ Support in English
💬 Leave your comment
Your opinion is important to us